わかっていそうでわかっていない原型の話(その2)
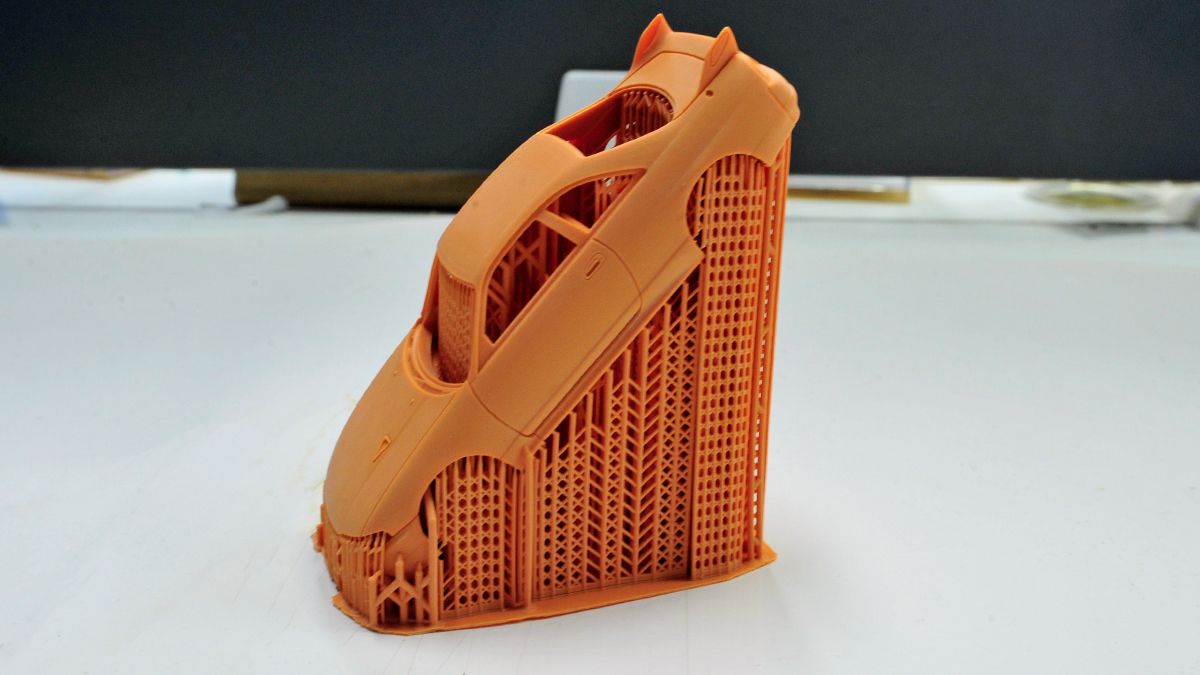
今から20年ほど前までは、事前に2次元で図面を引いて、それを元に原型師が無垢のケミカルウッドを削り出して原型を製作していました。様々な工具や測定機などを用いながら製作するので、手作業とは言え左右も対称ですが、ボディの面表現やプレスラインの深さなどは原型師の感性によるところが大きく、同じ車種であってもモデルカーメーカーによって違いがあり、それが“アジ”と表現されることもありました。
メイクアップではその後、3D CADで図面を作成し、それをNC旋盤で読み込んで切削で原型を製作している時期もありました。しかしNC旋盤の場合は切削する対象物に対して刃の角度が90度方向にしか入らないため、クルマのボディ形状を削り出すには、対象物を都度都度刃の向きに合わせて回転させなければならず、また場合によってはボディの原型を何分割にもして削り出す必要があるなど、形状の再現性はともかく、効率面でのメリットは多くありませんでした。
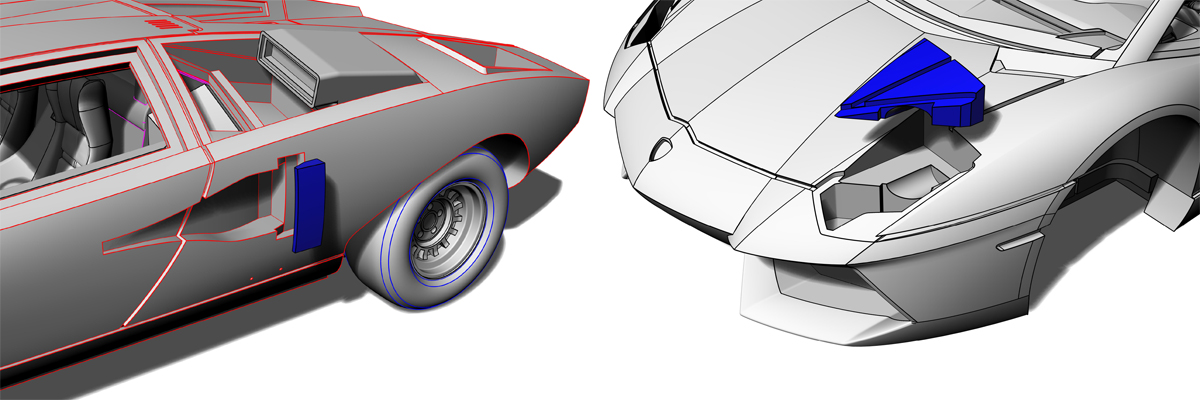
NC切削ではダクトやヘッドライトなど削れない箇所は分割し、あとからパーツを接着していた
現在は3D CADで原型を設計し、それを3Dプリンターで出力したものをマスター(一次原型)としています。とは言え3Dプリンターも5~6年前まではまだ万能とは言えず、積層跡がクッキリと残るために、それらを消去するために人間の手でやすり掛けを行ったり、あるいはその最中に失われたプレスラインのエッジを彫り直すなど、出力したものをそのまま原型に用いることはできませんでした。ところが現在では3Dプリンターの進化によって積層跡もほぼなくなり、ごくわずかな手直しでマスターとして使用できるようになりました。
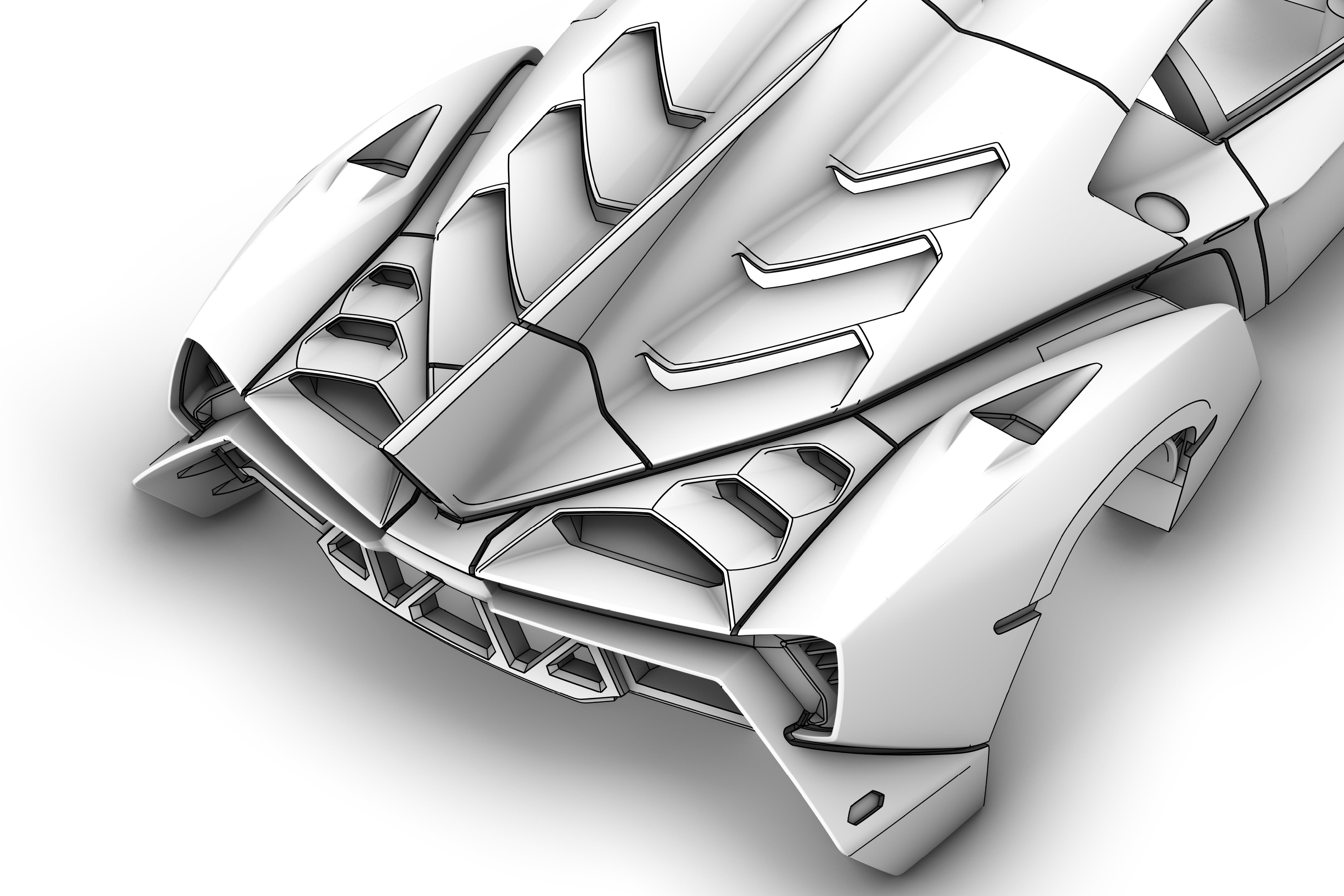
複雑な造形でも3Dプリンターであれば、パーツを分割することなくつくれる
今後も3Dプリンターの進化によって原型(マスター)の精度はますます向上していくと思われます。さらに進化が続けば、現在は原型から手作業で行っている生産型への置き換えは無くなり、型自体の原型を3Dプリンターで出力する時代がくるかもしれません。
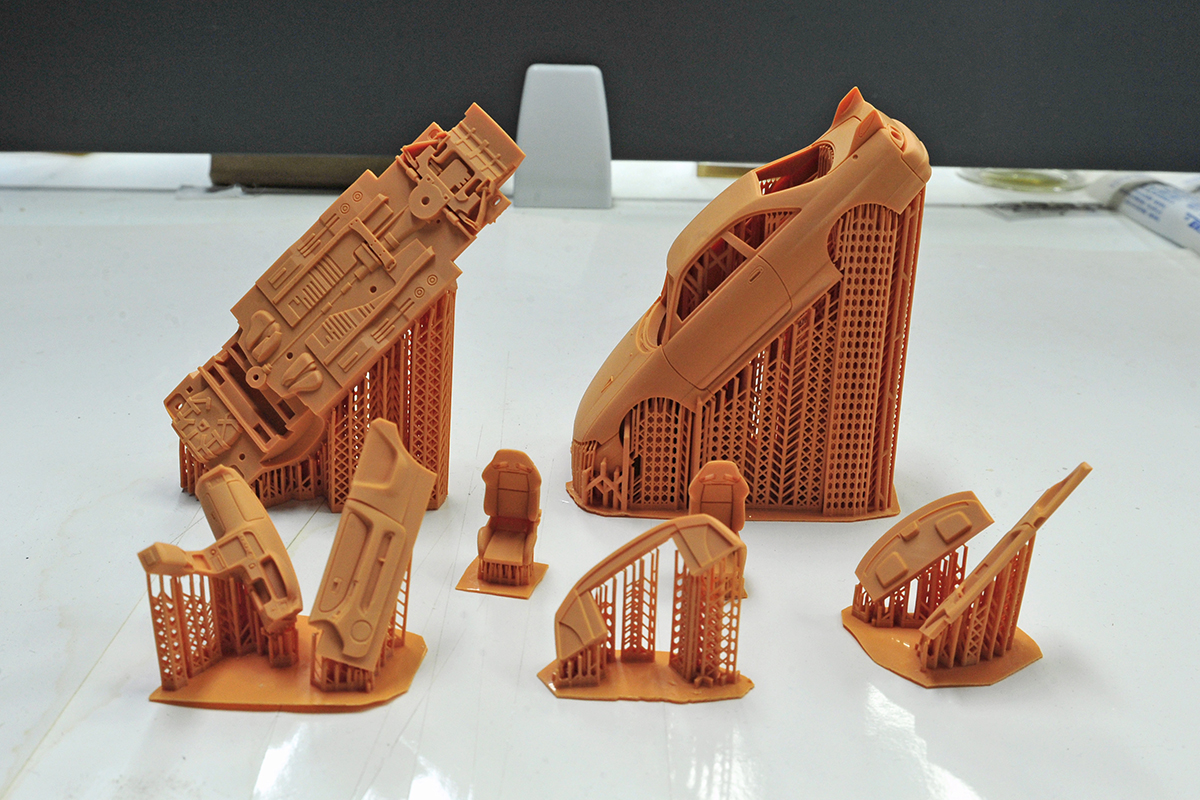
複数のパーツを一度にプリントアウトすることができるので、原型製作の時間を短縮できる
しかし、3Dスキャンや3D CAD設計が進化しても、例えばスケールに合わせた的確な面表現や省略すべきディテールなど、現時点ではまだまだAI(人工知能)では判断できない領域の作業はモデルカーの設計の過程には多く、エンジニアの感性や観察眼がモノを言うフェイズが続くことでしょう。
text : Makoto Ukai