わかっていそうでわかっていない原型の話(その3)
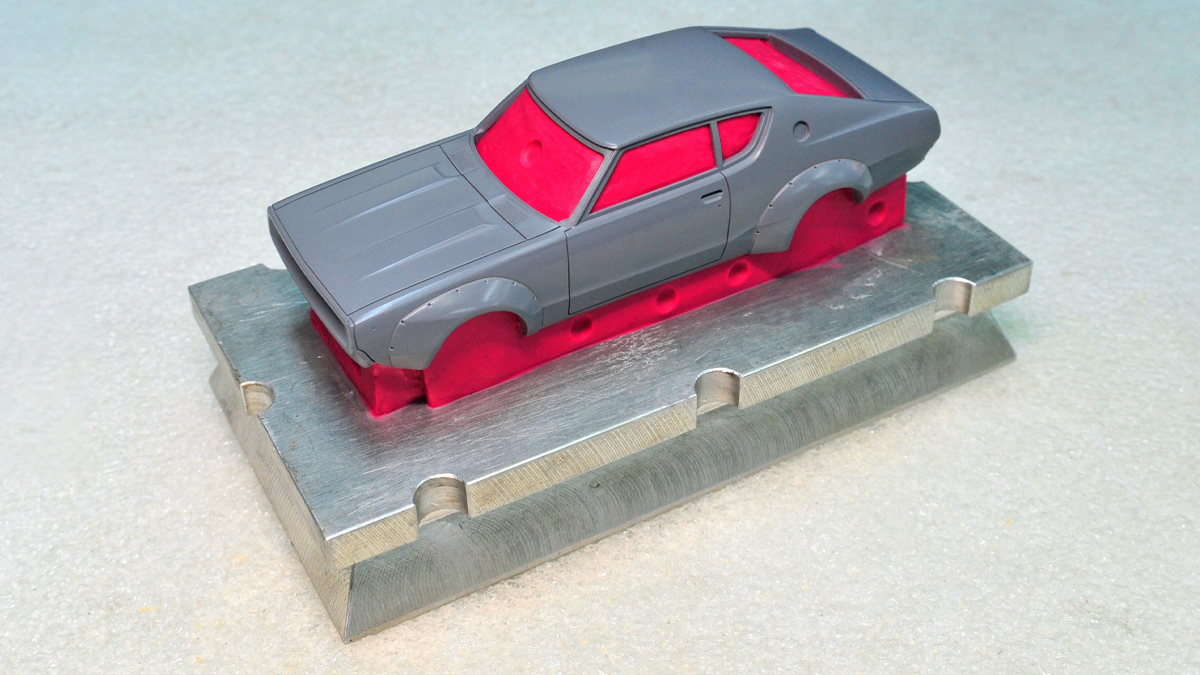
これまではモデルカーの原型(マスター)について書いてきましたが、ここからはそのマスターをいかにして生産用のシリコン型に置き換えるかについて説明していきます。ここではあくまでボディに限った話となりますが、細かな内外装パーツも概ね同じような手法で生産用の型を製作していきます。
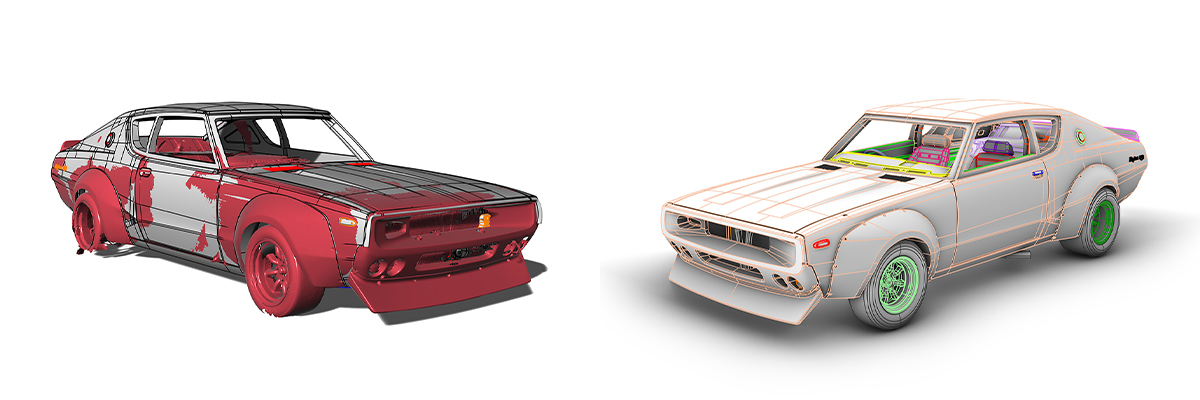
左:スキャンデータ(赤い部分) 右:設計データ
一番最初のステップとして実物の3Dスキャン、あるいは自動車メーカーから提供を受けた実車の設計データ(模型用に必要な情報を抽出する必要があります)を元に3D CADで原型データを設計します。これを3Dプリンターで出力したものがマスターとなります。
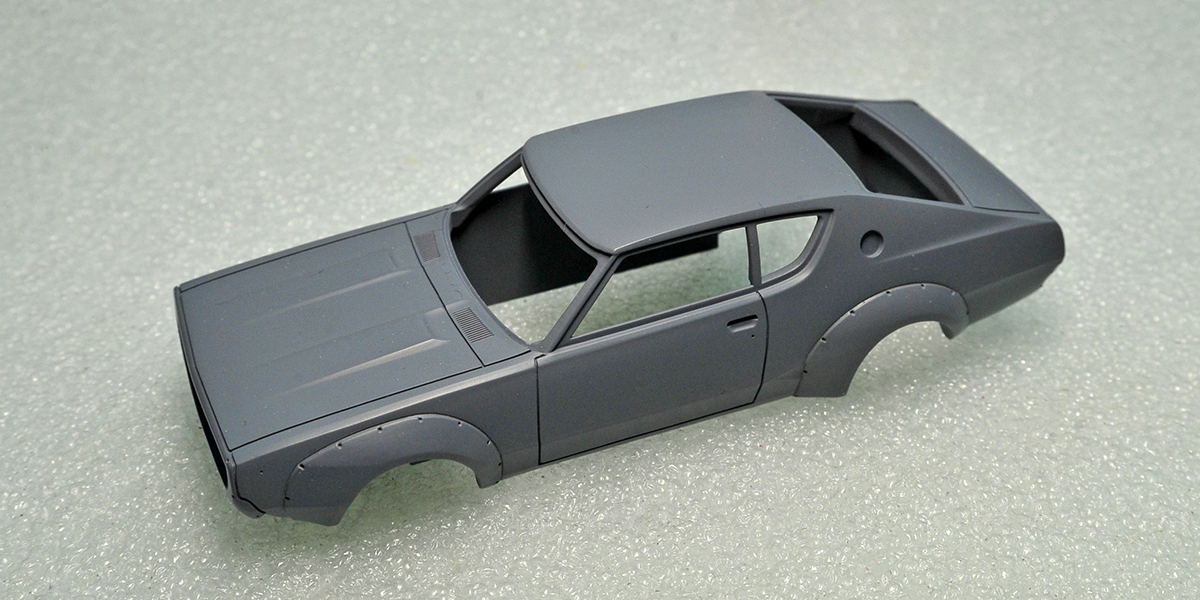
修正済ボディマスター(3Dプリントしたマスターの積層跡を消したり、パネルラインなどの微調整は手作業)
マスターを出力したら、次にそれを複製するためのメス型を作るための作業に入ります。と言っても、マスターから型を作り、その型で生産するわけではなく、型のまた複製を作ってそれで生産を行う方法を採ります。
型の製作は原型側にも負担がかかり、それを幾度も繰り返すと原型が破損する可能性もあるので、そのリスクヘッジが目的となります。
2次原型製作用のシリコン型
マスター(オス型)はまず生産用の2次原型(オス型:通称インショウ型)を製作するために、シリコン製のメス型に置き換えます。メス型は基本的に上下2分割となっており、逆に言えばクルマのボディを上下2分割して、なおかつ型から複雑な形状のボディが抜けるように造形しなくてはなりません。メス型は手作業で製作します。ボディの外形はトロトロのシリコンの中に漬け込んで、シリコンの硬化を待てば凹凸が逆転したメス型が出来あがることはイメージしていたけると思います。大まかなイメージではたい焼きがマスターで、焼き型がシリコン型となります。
しかし、モデルカーはたい焼きと違って例えばボディサイドのダクトや窓の抜けなど、中身が刳り抜かれ、側面部分にもモールドがあります。そのため単純にボディを上下2分割しただけでは型から成型したボディを外すことができず、型から成型物(≒ボディ)を取り外しやすい部分で型を分割する必要性が出てきます。
この型の分割線をパーティングラインと言います。型自体はシリコン製で、こじったり広げたりして成型物を取り外すことはできますが、それでもパーティングラインの設定は重要となるのです。
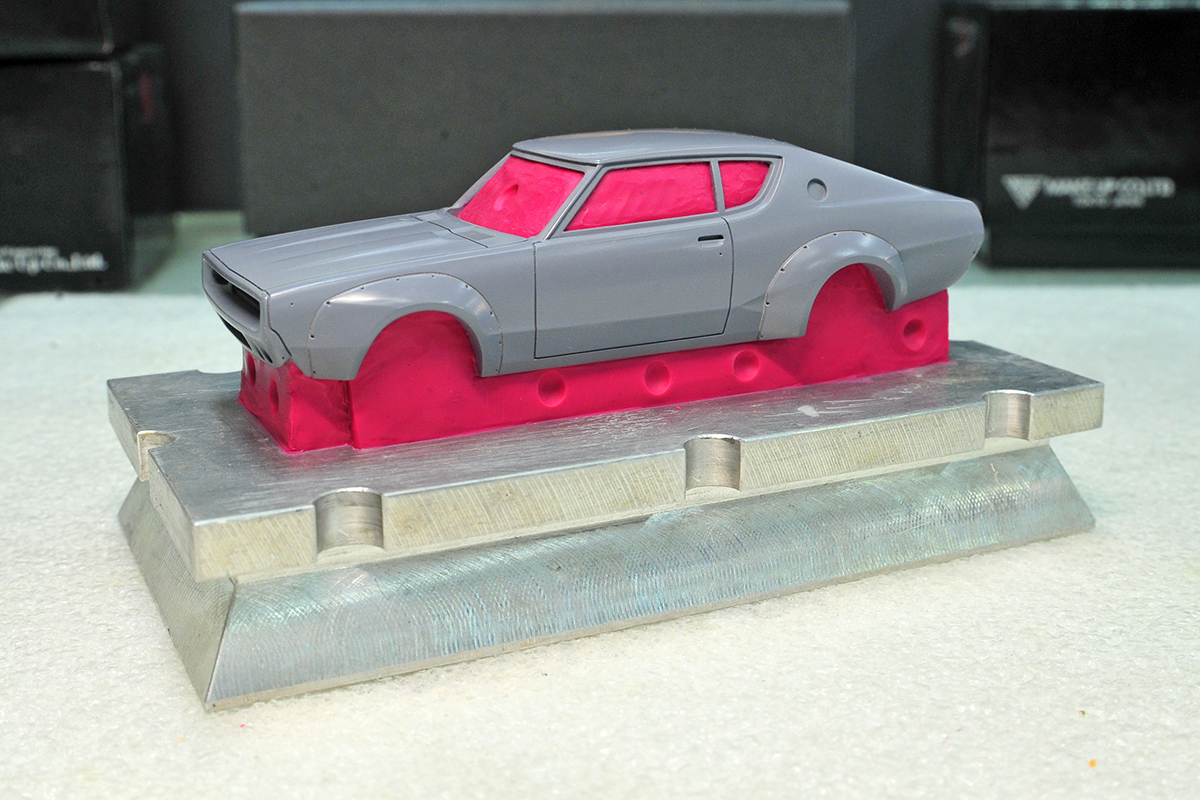
マスターと粘土の境目がパーティングラインになる
パーティングラインは成型物にも型の“合わせ目”として残ってしまうので、後処理も可能ですが、なるべくその必要がないような目立たない部分(サイドシル下など)に入るのが理想です。パーティングラインやボディ内側の肉抜きなどの設定は、硬化する粘土を盛って職人が手作業で行います。
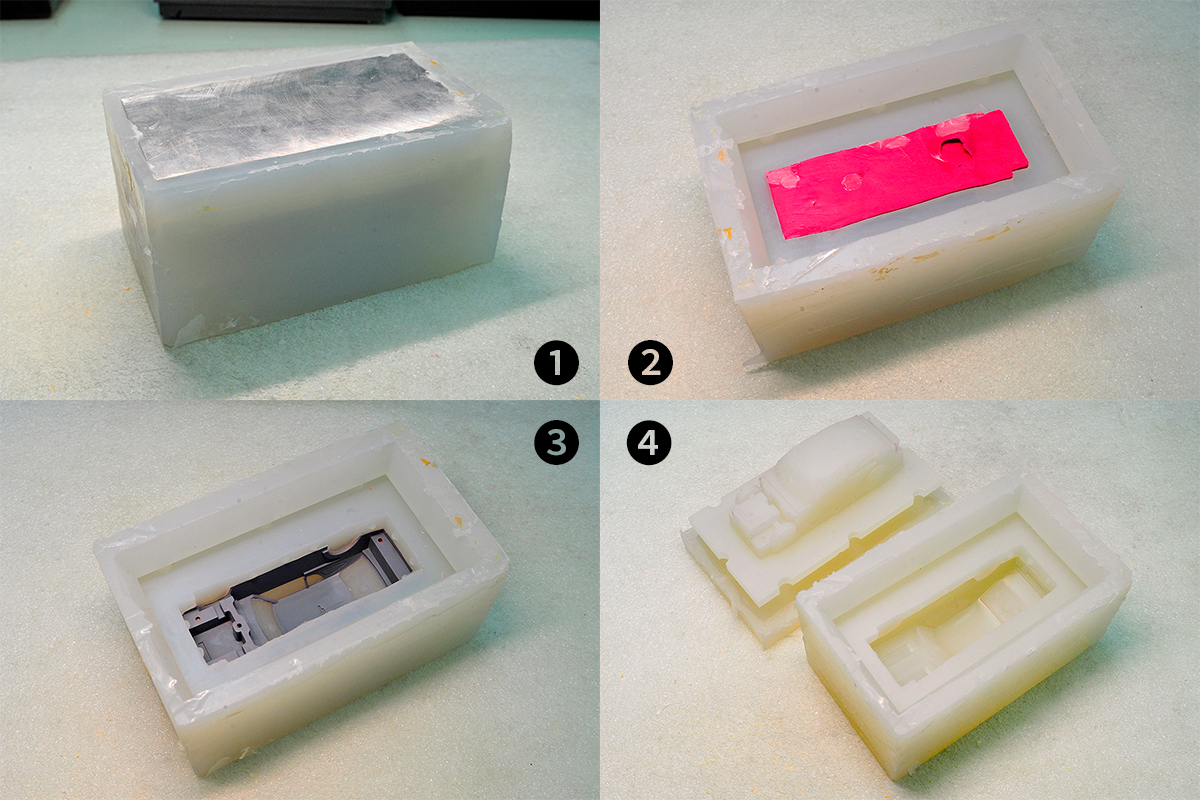
①:粘土を盛ったマスターにシリコンを流し硬化させたもの
②:土台(アルミ)を取り外し、粘土を取り除く
③:マスターはそのままでさらにシリコンを流し込む
④:③のシリコン型を取り外し、マスターを取り除くと2次原型作成用のシリコン型ができあがる
これで言わばオス型の原型(マスター)に次いでメス型のシリコン製マスターが完成したことになります。このシリコン製マスターを使って、今度は生産用の原型(インショウ型)を作ります。インショウ型に関しては材料を生産用のレジンではなく、収縮もなく硬度も高いレプロスロー(2液硬化のポリウレタン樹脂)で製作します。
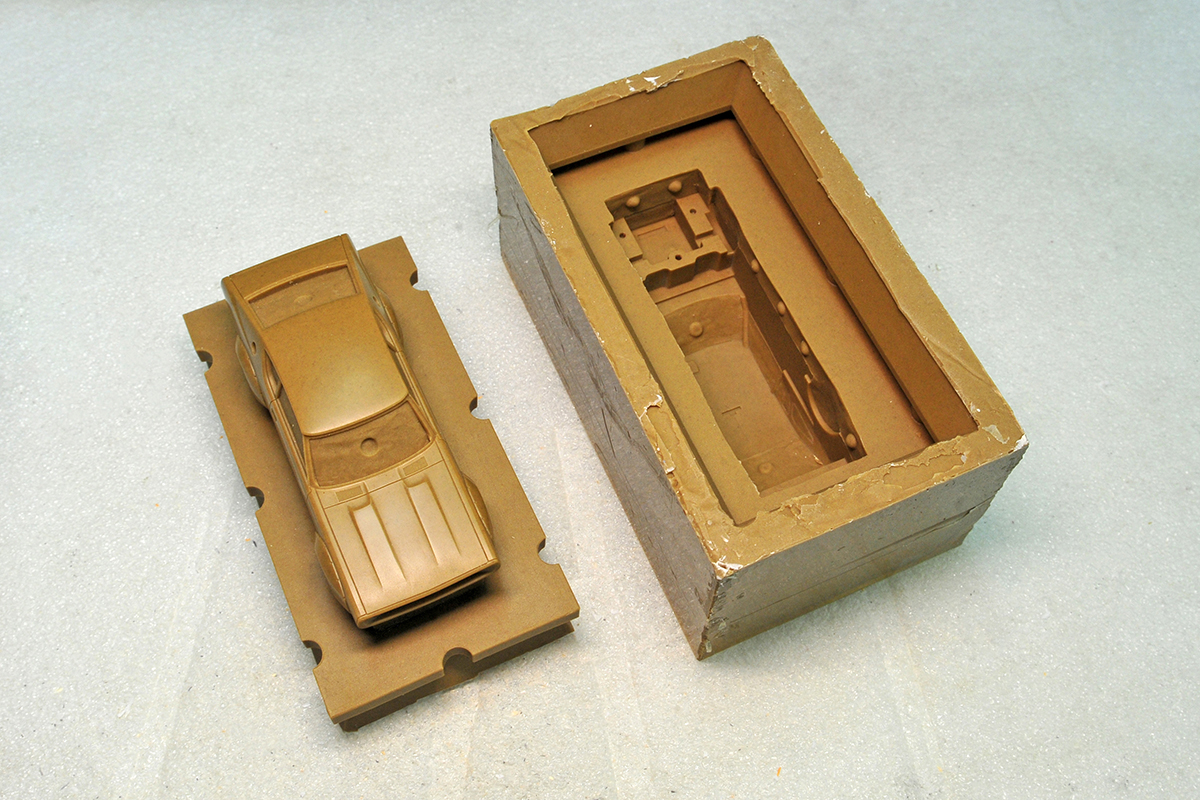
生産用シリコン型を複製するためのインショウ型
④のシリコン型にレプロスローを流し込んで作る
今度はインショウ型を使って生産用のシリコン型を複製します。生産用のシリコン型にレジンを流し込んで硬化させればモデルカーの量産が行えることになります。シリコン型は何度も成型を繰り返すと型が破断・欠損するため、メイクアップでは12台成型したら新しい型に取り換える方式を採っています。
余談ですが、例えばメイクアップのように0.3mmの深いパネルライン(溝)を刻んだボディを成型しようとすれば、型側には0.3mm以下の凸状のリブを設ける必要がありますが、これが少しでも欠損すれば溝が埋まり、ボディ側のパネルラインが分断することになります。型の耐性を上げようとすれば、パネルラインを太く浅くすれば良いわけで、また型が長持ち(ひとつの型でたくさんのボディを成型できる)することによってコストダウンを図れます。しかし、メイクアップではコストよりもモデルカーの精緻さを追求しているのです。
一概には言えませんが、レジン製のミニカーの原型の拘りを感じ取る基準として、“深く細いパネルライン”というのはひとつのポイントになるかもしれません。
text : Makoto Ukai